Reducing costs is a top priority in industrial engineering. Cost reduction strategies can significantly impact a company’s bottom line.
Industrial engineering focuses on optimizing complex systems, processes, and organizations. By applying cost reduction strategies, companies can achieve higher efficiency and productivity. Effective cost management leads to better resource utilization, minimizing waste, and improving overall profitability. Industrial engineers use various techniques to identify and eliminate unnecessary expenses.
This approach ensures that each dollar spent adds value to the operation. In this post, we will explore proven methods for cost reduction in industrial engineering. Understanding these strategies can help businesses stay competitive and financially healthy. Let’s dive into the key tactics that can transform your cost management approach.
Introduction To Cost Reduction
Industrial Engineering Cost Reduction is crucial for manufacturing and production. It ensures that companies remain competitive and profitable. By focusing on cost reduction, businesses can streamline processes, reduce waste, and improve efficiency. In this blog post, we will explore the importance and key principles of cost reduction in industrial engineering.
Importance In Industry
Cost reduction plays a vital role in the industry. Here are a few reasons why it is important:
- Increased Profit Margins: Lowering costs directly impacts profit margins. Companies can reinvest these savings into other areas of the business.
- Competitive Advantage: By reducing costs, businesses can offer competitive pricing. This attracts more customers and increases market share.
- Resource Optimization: Efficient use of resources reduces waste. It also helps in the optimal utilization of labor, materials, and machinery.
- Improved Quality: Streamlining processes often leads to better quality products. This enhances customer satisfaction and loyalty.
Consider the following table that illustrates the impact of cost reduction:
Scenario | Cost | Profit |
---|---|---|
Before Cost Reduction | $100,000 | $20,000 |
After Cost Reduction | $80,000 | $40,000 |
As shown, reducing costs from $100,000 to $80,000 doubles the profit from $20,000 to $40,000. This is why cost reduction is a key focus in industrial engineering.
Key Principles
There are several key principles in cost reduction:
- Lean Manufacturing: This principle focuses on eliminating waste and improving processes. By streamlining operations, companies can reduce unnecessary costs.
- Continuous Improvement: Also known as Kaizen, this principle emphasizes ongoing improvements in all areas. Small, incremental changes lead to significant cost savings over time.
- Value Analysis: This involves analyzing the function of products and processes. The goal is to find cost-effective alternatives without compromising quality.
- Standardization: Standardizing processes and materials reduces variability. It also simplifies training and maintenance, leading to lower costs.
- Automation: Implementing automated systems can reduce labor costs. It also enhances precision and efficiency in manufacturing processes.
These principles are the backbone of cost reduction strategies. They help companies to remain efficient and competitive.
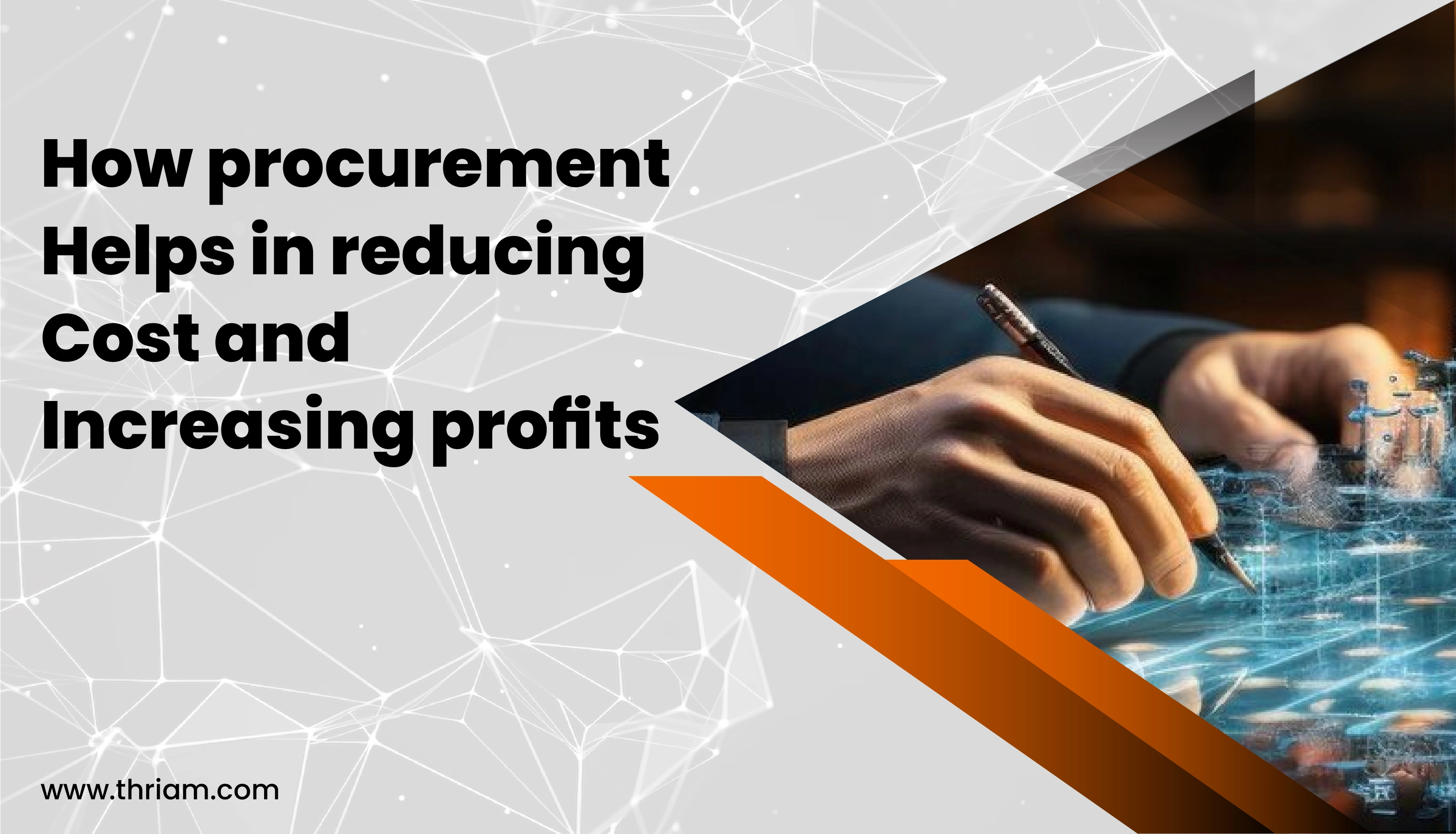
Role Of Industrial Engineers
Industrial engineering focuses on optimizing complex systems and processes. One of its primary goals is cost reduction. Industrial engineers play a crucial role in this area. They analyze, design, and manage systems to improve efficiency and reduce costs. Their expertise covers various sectors, from manufacturing to healthcare. By using their skills, companies can save money and improve productivity.
Skills And Techniques
Industrial engineers use a variety of skills and techniques to reduce costs. Their analytical skills are key. They often employ methods such as:
- Process Mapping: This helps visualize workflows and identify inefficiencies.
- Lean Manufacturing: Focuses on eliminating waste and improving flow.
- Six Sigma: A data-driven approach to reduce defects and variability.
- Time and Motion Studies: Analyzes work processes to optimize labor productivity.
Industrial engineers also rely on certain tools:
Tool | Purpose |
---|---|
Simulation Software | Models and tests process changes before implementation. |
ERP Systems | Integrates all facets of an operation, improving data flow and decision making. |
Statistical Analysis Software | Analyzes data for informed decision-making. |
These skills and tools enable industrial engineers to identify cost-saving opportunities. They can streamline operations and improve resource allocation. Their work often leads to significant cost reductions and enhanced efficiency.
Impact On Operations
The work of industrial engineers significantly impacts operations. By improving processes, they enhance overall efficiency. This leads to reduced operational costs and improved profit margins. Some key areas of impact include:
- Production Efficiency: Optimized workflows result in faster production times and lower costs.
- Resource Management: Better use of materials and labor reduces waste and cost.
- Quality Improvement: Fewer defects mean less rework and lower costs.
- Supply Chain Optimization: Streamlined supply chains reduce inventory costs and improve delivery times.
Industrial engineers also contribute to a safer workplace. They design ergonomic workstations and improve safety protocols. This reduces injury-related costs and enhances worker productivity.
Another significant impact is on customer satisfaction. Efficient operations lead to faster delivery times and better product quality. This improves customer satisfaction and loyalty.
Overall, the role of industrial engineers in cost reduction is vital. Their expertise leads to more efficient and cost-effective operations. This benefits both the company and its customers.
Analyzing Current Costs
Industrial Engineering Cost Reduction is vital for any business seeking to improve its bottom line. Analyzing Current Costs is the first step in this process. By understanding where money is spent, companies can identify areas for savings and improve efficiency. This analysis involves a detailed examination of all expenses, from raw materials to labor. Let’s dive into this crucial step.
Cost Breakdown
To analyze current costs effectively, a cost breakdown is essential. This involves listing all expenses and categorizing them. It provides a clear picture of where money is going. Here is a simple way to start:
- Direct Costs: These include raw materials, labor, and manufacturing supplies.
- Indirect Costs: These cover utilities, rent, and administrative expenses.
- Fixed Costs: Costs that do not change with production levels, such as salaries and equipment leases.
- Variable Costs: Costs that vary with production, like raw materials and direct labor.
A table can help visualize these costs:
Category | Example | Monthly Cost |
---|---|---|
Direct Costs | Raw Materials | $50,000 |
Indirect Costs | Utilities | $5,000 |
Fixed Costs | Salaries | $15,000 |
Variable Costs | Direct Labor | $8,000 |
By breaking down costs, businesses can pinpoint areas with high expenses. This step is crucial for identifying opportunities for cost reduction.
Identifying Waste
After understanding the cost breakdown, the next step is identifying waste. Waste can occur in various forms, such as:
- Material Waste: Excess materials that are not used in production.
- Time Waste: Idle time where employees are not productive.
- Process Waste: Inefficient processes that take more time or resources than necessary.
To identify waste, consider the following methods:
- Conducting Audits: Regular audits help find inefficiencies in processes and materials.
- Employee Feedback: Employees can provide insights into daily operations and waste areas.
- Analyzing Production Data: Data analysis can reveal patterns of waste in production cycles.
For example, if employees spend a lot of time waiting for materials, this is a clear indicator of time waste. If there are piles of unused materials, it points to material waste. By identifying these areas, companies can implement solutions to reduce waste and lower costs.
Lean Manufacturing Strategies
Industrial Engineering Cost Reduction is crucial for improving efficiency and competitiveness. One effective approach is Lean Manufacturing Strategies. These strategies focus on eliminating waste, optimizing processes, and enhancing productivity. By implementing Lean principles, businesses can reduce costs while maintaining high quality and customer satisfaction.
Principles Of Lean
The core principles of Lean focus on maximizing value and minimizing waste. These principles guide businesses to streamline their operations and improve overall efficiency. Here are the key principles:
- Value: Understand what value means to the customer and focus on delivering it.
- Value Stream: Identify all the steps in the value stream and eliminate those that do not add value.
- Flow: Ensure that the production process flows smoothly without interruptions or delays.
- Pull: Produce only what is needed by the customer to avoid overproduction.
- Perfection: Continuously improve processes to strive for perfection and eliminate waste.
Implementing these principles helps businesses to focus on activities that add value and eliminate those that do not. This approach reduces costs and improves efficiency.
Implementation Steps
Implementing Lean Manufacturing requires careful planning and execution. Here are the steps to follow:
- Identify Value: Determine what the customer values and focus on delivering it.
- Map the Value Stream: Analyze the entire process to identify and eliminate waste.
- Create Flow: Ensure a smooth workflow by minimizing interruptions and delays.
- Establish Pull: Produce products based on customer demand, not forecasts.
- Seek Perfection: Continuously improve processes to achieve higher efficiency and quality.
Each step builds on the previous one, creating a system that focuses on continuous improvement. Businesses can use tools like 5S, Kaizen, and Kanban to support these steps. Consistent monitoring and feedback ensure that the Lean principles are effectively integrated into the organization.
Six Sigma Methodology
In industrial engineering, reducing costs while maintaining quality is crucial. One effective strategy is the Six Sigma Methodology. This data-driven approach helps companies improve processes, reduce waste, and enhance efficiency. Let’s explore how Six Sigma can be a key tool for cost reduction in industrial engineering.
Dmaic Process
The DMAIC process is the core of Six Sigma. DMAIC stands for Define, Measure, Analyze, Improve, and Control. Each phase serves a unique purpose in improving processes and cutting costs.
- Define: Identify the problem or goal. Define customer requirements and project objectives.
- Measure: Collect data on current processes. Establish baseline measurements.
- Analyze: Examine data to identify root causes of problems. Use statistical tools to find patterns.
- Improve: Develop and implement solutions. Test changes to ensure they address root causes.
- Control: Maintain improvements. Monitor processes to prevent reverting to old ways.
Each phase is crucial for identifying inefficiencies and implementing effective solutions. By following DMAIC, companies can systematically reduce costs and enhance quality.
Benefits Of Six Sigma
Six Sigma offers numerous benefits for industrial engineering. These benefits lead to cost reduction and improved efficiency.
- Reduced Waste: Six Sigma identifies and eliminates waste. This leads to lower production costs.
- Improved Quality: Processes are optimized, resulting in fewer defects. Higher quality reduces rework and scrap costs.
- Increased Efficiency: Streamlined processes save time and resources. Efficient processes lower operational costs.
- Better Customer Satisfaction: Consistent quality and timely delivery boost customer satisfaction. Happy customers lead to repeat business and lower customer acquisition costs.
- Data-Driven Decisions: Six Sigma relies on data, not assumptions. Data-driven decisions are more accurate and effective.
These benefits make Six Sigma an invaluable tool for industrial engineers. Implementing Six Sigma can lead to significant cost savings and process improvements.
Technology And Automation
Industrial Engineering Cost Reduction involves finding ways to lower expenses while maintaining efficiency and quality. Technology and Automation play a crucial role in this process. They streamline operations and minimize human error. By integrating advanced technologies, industries can optimize resources and reduce costs effectively.
Role Of Ai
Artificial Intelligence (AI) is transforming industrial engineering. It helps in identifying cost-saving opportunities and improving operational efficiency. AI-driven analytics can predict maintenance needs, reducing downtime and repair costs.
Here are some key roles of AI in cost reduction:
- Predictive Maintenance: AI can forecast equipment failures. This helps in scheduling timely maintenance, preventing costly breakdowns.
- Quality Control: AI algorithms can detect defects in products. This reduces waste and ensures high-quality outputs.
- Supply Chain Optimization: AI analyzes supply chain data. It identifies inefficiencies and suggests improvements, lowering logistic costs.
- Energy Management: AI systems monitor and control energy usage. They optimize energy consumption, leading to significant cost savings.
Consider a factory that uses AI for predictive maintenance. The AI system collects data from machines, analyzes it, and predicts when a machine might fail. This allows the factory to perform maintenance before a breakdown occurs, saving both time and money.
Automation Tools
Automation tools are essential for cost reduction in industrial engineering. They help automate repetitive tasks, improve accuracy, and enhance productivity.
Some common automation tools include:
- Robotic Process Automation (RPA): RPA automates mundane tasks. It reduces human error and frees up employees for more complex work.
- Industrial Robots: These robots can perform tasks like welding, assembly, and painting. They work faster and more accurately than humans.
- Automated Guided Vehicles (AGVs): AGVs transport materials within a facility. They reduce the need for manual labor and improve safety.
Here’s a table showing the benefits of automation tools:
Automation Tool | Benefit |
---|---|
RPA | Reduces manual errors, increases efficiency |
Industrial Robots | Enhances precision, speeds up processes |
AGVs | Minimizes labor costs, improves safety |
Imagine a warehouse using AGVs for material handling. The AGVs transport goods from one end to another without human intervention. This reduces labor costs and enhances operational efficiency.
Employee Involvement
Industrial Engineering Cost Reduction is a crucial strategy for businesses aiming to enhance efficiency and minimize expenses. A key aspect of this strategy is Employee Involvement. Engaging employees in cost reduction processes can lead to innovative solutions and improved workplace morale. Their participation is essential for identifying inefficiencies and implementing practical changes.
Training Programs
Effective training programs are vital for engaging employees in cost reduction efforts. Proper training equips employees with the knowledge and skills needed to identify and address inefficiencies. Well-structured training programs can cover various topics, such as:
- Lean manufacturing principles
- Cost analysis techniques
- Quality improvement methods
- Energy-saving practices
Consider using a mix of training methods to cater to different learning styles. Workshops, online courses, and hands-on training sessions can all be effective. Interactive training sessions can engage employees better, helping them understand the importance of their role in cost reduction.
Here’s a simple table outlining a sample training program schedule:
Day | Topic | Method |
---|---|---|
Day 1 | Introduction to Lean Manufacturing | Workshop |
Day 2 | Cost Analysis Techniques | Online Course |
Day 3 | Quality Improvement | Hands-on Training |
Day 4 | Energy-Saving Practices | Interactive Session |
By investing in comprehensive training programs, companies can empower their employees to contribute effectively to cost reduction initiatives.
Feedback Mechanisms
Implementing feedback mechanisms is another vital aspect of employee involvement in cost reduction. Feedback allows employees to share their insights and suggestions for improvement. Regular feedback sessions can be conducted to gather valuable input.
Here are some effective feedback mechanisms:
- Suggestion Boxes: Place suggestion boxes in common areas to encourage employees to share their ideas anonymously.
- Surveys and Questionnaires: Distribute surveys or questionnaires to gather detailed feedback on specific processes or areas.
- Regular Meetings: Hold regular team meetings where employees can voice their concerns and suggestions openly.
- One-on-One Sessions: Conduct one-on-one sessions with employees to discuss their ideas and feedback in a more personal setting.
Creating a culture where feedback is valued can lead to significant cost savings. Employees often have firsthand knowledge of inefficiencies and can suggest practical solutions. Encouraging open communication ensures that valuable insights are not overlooked.
Consider implementing a reward system for the best suggestions. Recognizing and rewarding employees for their contributions can motivate them to actively participate in cost reduction efforts.
In summary, effective feedback mechanisms can provide valuable insights and foster a culture of continuous improvement, ultimately leading to significant cost reductions.
Measuring Success
Industrial engineering focuses on optimizing complex processes and systems. Cost reduction is a key goal in this field. Measuring success in cost reduction is essential. It helps businesses understand if their efforts are effective. This involves tracking various metrics and making continuous improvements.
Key Performance Indicators
Key Performance Indicators (KPIs) are crucial for measuring success in industrial engineering cost reduction. KPIs provide clear metrics to track progress. They help identify areas needing improvement. Here are some important KPIs:
- Cost Savings: Measure the total amount saved over a specific period.
- Productivity Rates: Track the output per labor hour.
- Waste Reduction: Monitor the decrease in material waste.
- Cycle Time: Measure the time taken to complete a process.
- Quality Improvement: Track the reduction in defects or errors.
These KPIs offer valuable insights into the efficiency of cost reduction efforts. For instance, if productivity rates increase while costs decrease, it indicates successful optimization. Using a table can help in tracking these KPIs over time:
KPI | January | February | March |
---|---|---|---|
Cost Savings | $10,000 | $12,000 | $15,000 |
Productivity Rates | 80 units/hr | 85 units/hr | 90 units/hr |
Waste Reduction | 5% | 4.5% | 4% |
Cycle Time | 10 min | 9 min | 8 min |
Quality Improvement | 3% | 2.5% | 2% |
Tracking these KPIs regularly helps businesses stay on course. It ensures that cost reduction strategies are effective and sustainable.
Continuous Improvement
Continuous improvement is a core principle in industrial engineering. It means constantly seeking ways to enhance processes. This approach ensures that cost reduction is not a one-time effort but an ongoing process. Here are some methods to promote continuous improvement:
- Kaizen: A Japanese term meaning “change for the better.” It involves small, incremental changes.
- Lean Manufacturing: Focuses on minimizing waste while maximizing productivity.
- Six Sigma: A set of techniques aimed at improving quality and reducing defects.
Implementing continuous improvement involves several steps:
- Identify areas needing improvement.
- Analyze the current process.
- Develop solutions for improvement.
- Implement the changes.
- Monitor the results and adjust as needed.
Continuous improvement fosters a culture of excellence. Employees are encouraged to suggest improvements. Regular training and workshops can help embed this culture. Benefits of continuous improvement include:
- Increased efficiency and productivity.
- Reduced costs and waste.
- Improved quality and customer satisfaction.
- Enhanced employee engagement and morale.
By focusing on continuous improvement, businesses can achieve lasting cost reduction. It ensures they remain competitive and agile in a dynamic market.
Industrial Engineering Cost Reduction In Bangladesh
Industrial engineering cost reduction focuses on minimizing expenses while maintaining or improving product quality and efficiency. In Bangladesh, this practice is gaining traction as industries strive to stay competitive. By implementing effective cost reduction strategies, companies can enhance their profitability and ensure sustainable growth.
Industrial Engineering Consultancy Bangladesh
Industrial engineering consultancy in Bangladesh offers expert guidance to help businesses reduce costs. These consultancies analyze current processes, identify inefficiencies, and suggest improvements. Here are some key services they provide:
- Process Optimization: Streamlining operations to reduce waste and improve efficiency.
- Resource Management: Efficient use of materials and labor to cut costs.
- Technology Integration: Implementing advanced technologies to enhance productivity.
- Quality Control: Ensuring high-quality output while minimizing defects and rework.
Consultancies also offer tailored solutions based on the specific needs of a business. They conduct thorough assessments and provide actionable insights. Some of the leading industrial engineering consultancies in Bangladesh include:
Consultancy | Services |
---|---|
ABC Consultancy | Process Optimization, Resource Management |
XYZ Solutions | Technology Integration, Quality Control |
Bangladesh Engineering Experts | Comprehensive Industrial Engineering Services |
These consultancies help businesses in Bangladesh achieve significant cost reductions. They ensure that companies remain competitive in the global market.
Contact Us
If you need expert guidance on industrial engineering cost reduction, contact us. Our team of experienced consultants is ready to assist you. We offer personalized solutions tailored to your business needs. Here’s how you can get in touch with us:
- Email: engineering@bestlubri.com
- Phone: BD:+880-167-5000 US: +14094542317
- Initial consultation to understand your requirements.
- Detailed process analysis to identify cost-saving opportunities.
- Implementation of customized solutions to reduce costs.
- Ongoing support to ensure continuous improvement.
Reach out to us today to start your journey towards cost-efficient operations. Let our expertise help you achieve your business goals.
Frequently Asked Questions
How Do Industrial Engineers Contribute To Cost Reduction In Production?
Industrial engineers streamline production processes, reduce waste, and improve efficiency. They optimize resource utilization and implement cost-effective technologies. Their efforts lower operational costs and increase productivity.
How To Reduce Engineering Costs?
Reduce engineering costs by optimizing designs, using cost-effective materials, and improving project management. Automate repetitive tasks and outsource non-core activities. Implement lean manufacturing principles and invest in employee training.
What Is Costing In Industrial Engineering?
Costing in industrial engineering involves analyzing and controlling production costs. It helps optimize resources, improve efficiency, and maximize profitability.
How To Do Cost Reduction In Manufacturing?
Optimize processes, reduce waste, and automate tasks to cut manufacturing costs. Negotiate supplier contracts and use energy-efficient equipment. Train employees to improve productivity.
Conclusion
Cost reduction in industrial engineering leads to significant savings. Effective strategies help streamline processes and minimize waste. This boosts productivity and profits. Every business, big or small, benefits from these practices. Implement these tips and see noticeable improvements. Keep assessing and refining your methods.
Small changes can have a large impact. Stay committed to cost reduction for long-term success. Efficient operations benefit everyone.